Topics
Mission Impossible: Finding the Right ERP System
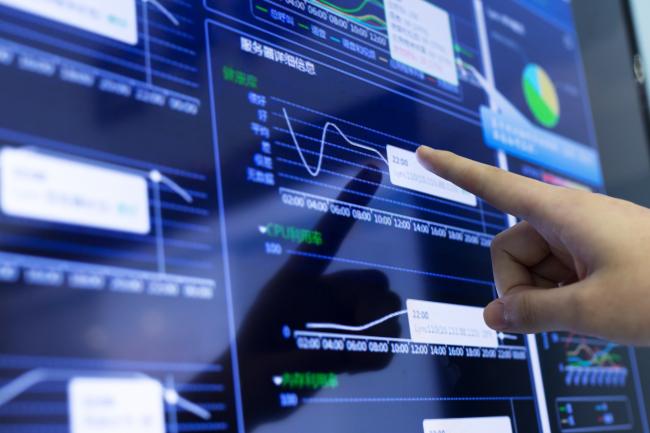
While my previous entry was inspired by the advertising for an upcoming theatrical movie, this one is based more on conversations I have had with prospects and customers about their businesses, where this popular movie title sort of spring to mind.
Intro to the soft goods industry
Over the years, I have repeatedly pointed out that the soft goods industry is not rocket science; rather, it's a matter of dealing with an infinite number of infinitesimal details that need to be tracked at all times. Specialists in other areas of manufacturing, such as automobiles, have commented to me that their industry has nothing on us when it comes to complex business processes in dealing with so much minutia.
Why all the complexity?
It is readily apparent that a major source of this complexity has to do with the fact that the products we make come in multiple sizes and colors, each with its own particular specifications for certain aspects. For example, while both the size 2 and size 10 dresses might both require the same rayon fabric, one obviously consumes more material than the other - a reality that must be taken into account when one calculates how many total yards are needed for production cut. In addition, the size of the yoke, armhole and most of the other detailed measurements will usually differ from one size to the next, making for even more detail to track.
If all one produced was a single style of dress that came in one or two colors, this might all seem fairly trivial. However, when scaled up to dozens or hundreds of styles that represent hundreds or thousands of SKUs it becomes a rather daunting job to keep a track of what raw materials are needed and, for that matter, when they are needed once allowance is made for the time to manufacture and the required time to deliver.
Even a seemingly simple business process, such as selling embellished T-shirts made from completed blank shirts bought from an outside vendor, can become a difficult row to hoe if numerous finished shirts are derived from the same colored blank tees. That is, if a dozen styles of embellished T-shirts (I.e.-finished goods) come in red and use the same blank T, maintaining a track of the inventory of red blanks and requirements of ordering them can get very complex very fast, particularly when there are four or six or eight sizes to be accounted for as well.
An appropriate BOM
I have seen numerous T-shirt companies finding themselves having a tremendously difficult time keeping track of their raw materials (that is, the blank T-shirts). I have to explain to them that the reality of their situation is that they have to have a bill of materials (BOM) for their finished products. Naturally, this BOM must ascribe the appropriate color and size of T-shirt to each finished item-a size medium finished red T-shirt we require a size medium red blank.
There is really no escaping this without such BOMs the MRP calculation cannot ascertain how many of what color and size blanks are needed based on a sales forecast or actual sales orders in the pipe. The good news with BlueCherry is that once a BOM is created for the blue style 100 finished shirt, making a copy of that BOM and altering one field to indicate it's for the style 200 finished shirt is simplicity itself.
The value of the right ERP system
The value of a soft-goods specific ERP system such as BlueCherry is that it is designed to handle precisely all those details, and more. Of course, for a manufacturer or distributor who deals in products that don't come in sizes and colors, BlueCherry still offers tremendous power in the realms of allocating supply to demand, working with vendors and customers via EDI and, in general, enabling one to run the business on a management by exception basis. But for folks making clothing or footwear, BlueCherry is particularly useful.
And the "mission", of ensuring that enough of the proper sizes, styles and colors are produced at the right time to meet customer demand, is much less "impossible".